Mine or cavity grouting generally uses a low strength cement based grout to fill large natural or man- made voids.
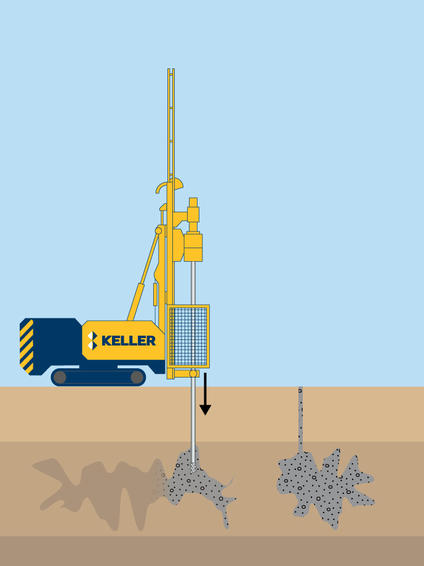
Common uses
Process
Bulk infill grouting is normally carried out from primary grout injection holes on a square grid with secondary and tertiary holes as required.
Typically the grouts incorporate pulverised fuel ash as a ‘filler’ to the grout mix, the material being usually available in mining regions. The mixes may include Sand and Bentonite etc as required.
Depending on the nature of the void and the filling requirements the process may involve the construction of containment barriers. These are typically formed using gravel or a very low mobility grout placed from the surface in closely placed pre-drilled holes. In collapsed workings or naturally contained voids a higher mobility grout is placed without the need for containment barriers.
Recently, we have developed and implemented an economic and efficient PFA free bulk grout that can be used when the potential environment risks of a some PFA based grouts are not acceptable.
Advantages
Quality assurance
We have extensive knowledge of grout mixes, tested and used extensively in Australia and overseas with a track record of performance. Our robust inspection and testing protocols ensure that our site mixed grout met the project requirements
We rely on this experience to develop grout mixes for local projects that incorporate the most economically available local materials.
The major mine infilling grouting works we have undertaken have allowed us to innovate the testing process further. Rapid 3D borehole positioning system allow us to accurately target deep voids, high quality down hole cameras provide visual evidence of grouting and roof contacts, acoustic viewers allow us to visual abandoned seams even in turbid flooded workings.