Permeation grouting, also known as cement grouting or pressure grouting, permeates coarse, granular soils with flowable particulate grouts to create a cemented mass.
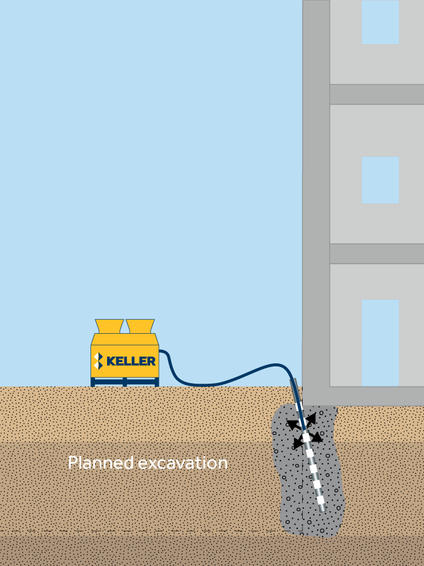
Common uses
Process
Depending on the conditions, general purpose cement or microfine cement grout is injected under pressure at strategic locations through single ‘port’ or multiple ‘port’ pipes. These pipes are often referred to as tube-a-manchette or TAM. The grout particle size and void size must be matched properly to allow the cement grout to permeate. For some temporary applications a chemical solution-based grout, often based on Sodium Silicate, is used as it provides improved flow characteristics. The grouted mass has an increased strength, stiffness, and reduced permeability.
Advantages
Quality assurance
Keller has provided permeations grouting solutions for decades. Its fleet of low headroom, tight access rigs minimises disruption to normal facility operations. Automated digital systems can also be used to monitor and record flow rates, grout volumes and grout pressures ensuring the grouting specification is achieved.